Controlled Torque Requirements Make The Hydrauc Wrench A Tool Of Choice In Industries and Large Projects
Development Of The Hydraulic Wrench
A hydraulic wrench is used to fasten and unfasten nuts and bolts. There can be no doubts about the importance of nuts and bolts in the manufacture and maintenance of machinery and equipment.
It is also a proven and recognized fact that the incorrect use of these vital fasteners can lead to severe maintenance problems; even disasters at times.
A close study fastening methods and devices led to the evolvement of torque wrenches. For many years the only tools available were manual torque wrenches to apply correct force for bolting applications. Then the first half of the 1970s experienced an increased trend towards improving worker productivity engaged in bigger projects posing new technological challenges. The resulting necessities led to the development of the hydraulic wrench for correct and controlled torque application to bolted connections.
Constraints of working in confined and cramped spaces, undersea operations, novel metallurgy and speed of work all catered to the fast increase of the use of hydraulic wrenches. With the use of these versatile tools, assembly and maintenance crews can apply thousands of ft.lbs pressure to tighten or loosen very large size nuts and bolts even in precarious locations. During disassembly, fasteners virtually jammed solid due to corrosion can also be loosened/broken with extreme ease using this tool.
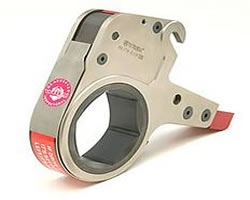
Hydraulic Wrench Design
The design of the hydraulic wrench transforms lenier hydraulic motion into an arcing motion in order to facilitate opening and tightening of fasteners. The inline hydraulic wrench is designed to carry a drive pawl, drive gear/ratcheting wheel, the body which houses the hydraulic cylinder and the reaction device which bears against an adjacent object to prevent the wrench from pulling off the bolt during operation. The hydraulic wrench is supplied with pressurized hydraulic fluid from a hydraulic pump driven either by an electric motor or through pneumatic pressure.
The pump is usually a compact portable unit and is connected to the wrench through high-pressure hoses; connectors at the wrench end are designed to swivel 360 degrees to let the wrench be positioned for operation at different angles.
The pressurized fluid supplied to the cylinder of the wrench mechanically operates the drive pawl through a lever arm attached to the piston in the cylinder.
The drive pawl delivers torque to the ratcheting wheel. The wheel has a square or other suitably shaped drive head to which a socket/box spanner etc. can be attached for opening/tightening a fastener.
Factors Governing Torque Delivery Of A Hydraulic Wrench
There are three factors that mainly govern the power characteristics of a hydraulic wrench: the fluid pressure in the cylinder, the arm length of the wrench and cylinder position. How far reaching are the effects can understood by treating a comparison of two different model of hydraulic wrenches manufactured by Enerpac as a typical example.
Enerpac model W15000 of the LP series can deliver a maximum torque of 15000 Ft.lbs at a pressure of 10000 psi whereas at the same pressure Model S25000 of series S is capable of delivering 25400 Ft.lbs. The operating pressure is adjustable in all the models within a specified range to suit needs of specific applications. The pressure is delivered to the wrench through the hydraulic fluid supplied by the pump connected to the wrench.
The pumps are usually powered by an electric motor of suitable size. However, in working conditions where an electric spark can be hazardous, pneumatically powered hydraulic pumps are employed. Keeping in view the need for working in hard to reach places constant technological efforts are leading to the development of easily portable light weight pumps.
The formidable fluid pressure these pumps can build during their working cycles and the pressure variations demanded by different operating conditions compels a pressure regulation device to be incorporated in the pressure circuit. This finds shape in the form a relief valve mounted on the pump unit as a damage control measure.
This is set to open at a predetermined pressure and allows fluid to flow back to the reservoir to maintain specified pressure in the circuit. There are also controls on the wrench that let the user regulate torque delivery within preset limits for bolting operations.
Accuracy In Torque Delivery Is A Basic Characteristic Of A Hydraulic Wrench
Hydraulic wrenches are geared to cater to the high degree of precision required in bolting equipment and machinery incorporating complex technological design and material composition. These wrenches provide accuracy tolerances of + 1/2 to - 3% which is far above the pneumatic or electric power wrenches.
Productivity is also increased tremendously and is dependent upon the flow of the pressurized fluid from the pump unit. It is directly related to the volume required for extension and retraction of the hydraulic cylinder, which in turn governs the amount of rotation delivered to the nut/bolt with each stroke of the cylinder.
An increase in the hydraulic flow to the cylinder would increase the rotational speed saving overall time in the operation. Therefore a pump with a higher flow rate would cut down many crucial worked hours. However, the pump would need to be optimally sized vis a vis the bolting operations.
To understand why correct torque application (which is a characteristic feature of hydraulic wrenches) is so important one needs to look into the technical aspects of bolting operations which in fact are far from simple.
101 Of Bolting
A bolt/fastener is designed to fulfill the purpose of bringing together two mating pieces of equipment. The force exerted on the joint by clamping is due to the preload that is generated by torquing the bolt to rotate it to effect tightening or loosening.
The threads of the bolt offer resistance against the threaded grooves in its hole/nut, literally stretching the bolt to a certain extent. With an inherent tendency to return to its original position, the bolt exerts pressure through its head or the nut to clamp the two pieced together.
Critical and complex fastening applications rely upon tightening of bolts within specifications related to the material of the bolt, the material being fastened together and functional performance of the equipment. Vibration can make a 'too little tightened' bolt to shake loose and cause a structural support member to break apart or cause leakage(s) in flange gaskets in pipelines. Tightening a bolt too much can cause immense stress that can eventually lead to bolt breakage.
From the discussions above, the importance of precision required in bolting operations becomes very clear. Hydraulic torque wrenches provide the means of near perfect control of tightening torque making them tools of choice as compared to other uncontrolled methods of bolt tightening such as sledge hammers and striking wrenches or pneumatic wrenches that are devices with limited control.
|